Technical fabrics usually benefit from being stronger and lighter. These properties become essential – and potentially lifesaving – when applied to high performance protective sports apparel. Dyneema® Composite Fabrics can also be engineered to take on a whole range of other properties – including breathability, waterproofness, conductivity and color.
WHAT ARE COMPOSITES?
Always the result of at least two components, composites come in many forms. For example, concrete is a composite. But so are the sophisticated fusions of resin and fiber used by the aerospace industry.
Flexible fabric composites involve fusing fabrics, fibers and surface coatings, which gives the resulting fabric tailored properties – may it be breathability, waterproofing or resilience against UV light. In other words, a composite fabric involves bringing together various layers to achieve a specific purpose.
WHAT CAN YOU DO WITH DYNEEMA COMPOSITE FABRICS?
Fifteen times stronger than steel, but floats on water, Dyneema® is world’s strongest, lightest fiber and has long been used to moor oilrigs, stop bullets and repair human ligaments.
As a fabric component, Dyneema® technology was first applied to sailcloth for the winning yacht of America’s Cup 1992. Since then, Dyneema® Composite Fabrics have been engineered with a whole range of different properties (breathability, colors, solar reflectivity, various sensor and telecommunication abilities, etc.) and for many different applications (airships, ultra-light hiking equipment, heart valves, flexible circuitry, etc.). Currently, Dyneema® Composite Fabrics are inspiring a revolution in the protective sports apparel industry.
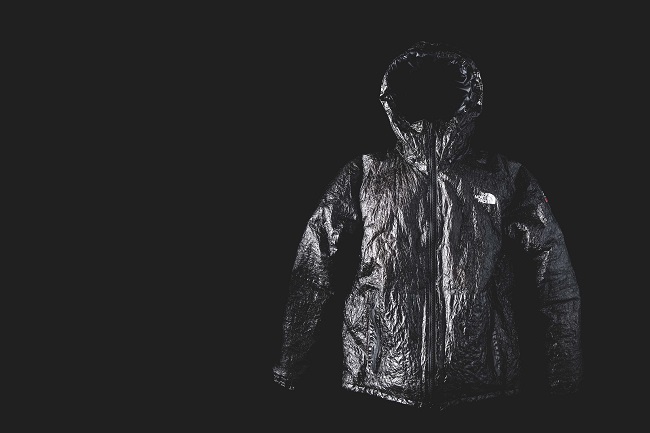
is the original inventor and manufacturer of the Ultra High Molecular Weight Polyethylene (UHMWPE) fiber branded as Dyneema® and has decades of experience applying the fiber in sheets, tapes and the world’s strongest, lightest and most engineered fabrics and composites.
With finished weights ranging from 11 gsm to over 500 gsm, customers choose Dyneema® Composite Fabrics when they need a low weight, high tensile strength, high modulus material for the most demanding applications – whether it’s alpine or motocross. The fabric’s potential is only limited by imagination.
“The way Dyneema® creases and takes on personality and shape with time and use – it reflects that of its environment and the user’s experience.” – Alasdair Leighton-Crawford (CIMORO)
HOW DOES IT WORK?
Dyneema® Composite Fabric can be regarded as a “high-tech sandwich” of sorts. For example, the original sailcloth had a mix of UHMWPE and carbon fibers as filling, which was then fused with two outer layers of polyester film in a high-pressure autoclave – highly loaded areas of the sails would get an extra dash of graphite fibers.
Today, the fabrics are constructed from various oriented fiber layers and many types of high performance films or surface coatings. Multiple oriented fiber layers may be positioned at any angle (2D and 3D) resulting in an unlimited range of fiber area weights and unlimited fiber choices and combinations. For example to synergize properties, Dyneema® can be combined with carbon for high modulus, low weight, flex fatigue and crack resistance.
The choice of polymer composition and the possible inclusion of a wide range of additives can affect the resulting fabric’s color, conductivity, and flammability among other properties.
The choice of surface coatings can influence the resulting fabric’s overall toughness, gas permeability, low/high temperature operating capability, visible light/UV/IR characteristics, surface texture, bond ability, waterproofness, surface conductivity and breathability. Because of the nature of their construction, Dyneema® Composite Fabrics have predictable and linear properties critical for engineering designs.
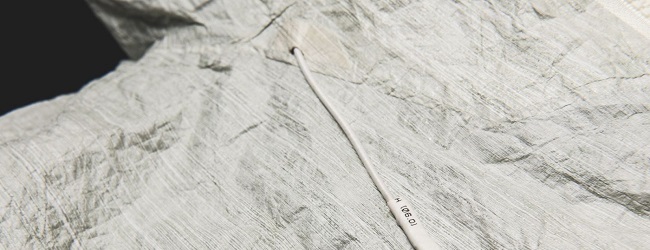
CUSTOMIZED SERVICES
DSM Dyneema has an experienced in-house team capable of collaboratively developing customized products based on a client’s specific needs. We can also provide a roadmap to scaling-up production.
BONDING: Bonding by means of pressure sensitive adhesive (PSA) is an ideal way to construct with many different Dyneema® Composite Fabrics – whether it’s for a garment, tent or bag. The result is a seam that’s both waterproof and strong. DSM Dyneema is also able to direct clients to best-of-the-class manufacturers so trial-and-error is no longer necessary.
CUSTOM COLORIZATION: DSM Dyneema offers the option of customized prints, whether with patterns and/or solid colors. There are several different ways of coloring Dyneema® Composite Fabrics, each with its own look and feel.
- Solid Color process: Adding dye to the inside layers of the composite. Lighter fabrics will have lighter color and saturation; heavier fabrics will have deeper color saturation.
- Sublimation printing: Currently only for fabrics with K.18, WOV 6 and WOV 32c (polyester surfaces). Colors: Black, Tree-leaf Camo, Olive Drab, Blue, Orange and Gray.
- Applying a pre-patterned woven or film as the outside layer of the composite.
DSM Dyneema also offers the option of customized prints (pattern and/or color). Do you have anything specific in mind? Let us facilitate it.
LAMINATION: We build fabrics – we don’t weave them. Dyneema® Composite Fabrics can be laminated with a range of other fabrics or materials, resulting in completely new fabrics with unique properties. The possibilities are literally endless.